Comparing MIG Welds and Stick Welds: Which is Stronger?
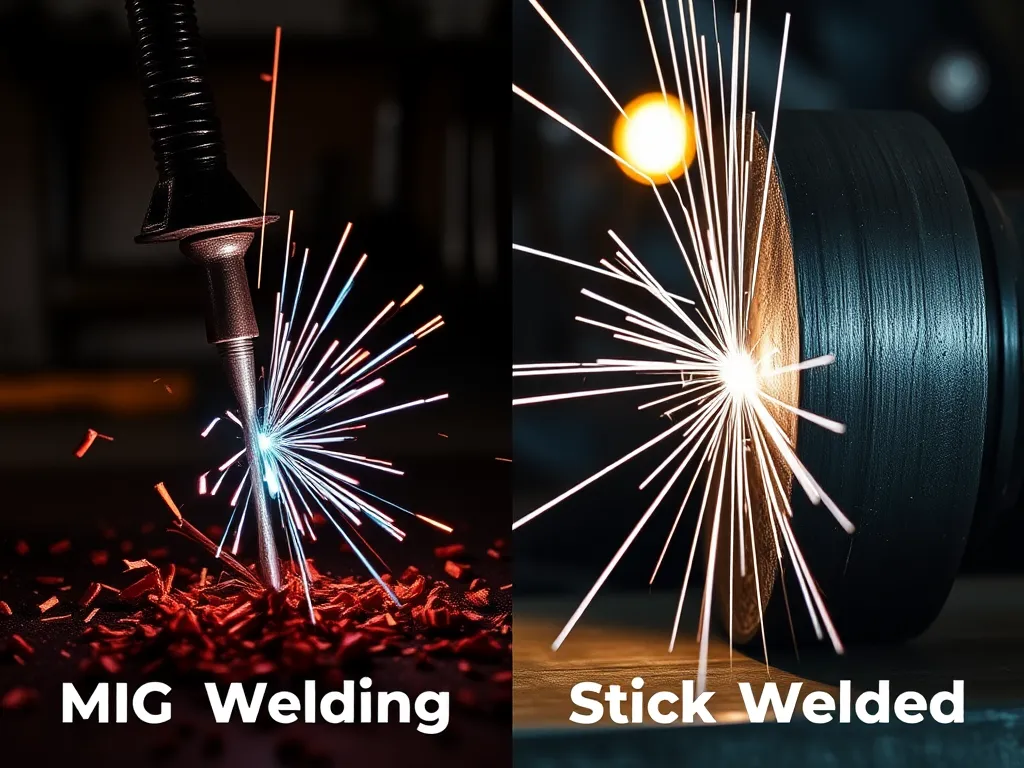
Welding Techniques: An In-Depth Guide
Welding techniques are essential processes utilized in metal fabrication, manufacturing, and construction, which involve joining materials, usually metals or thermoplastics, by using heat, pressure, or a combination of both. The field of welding encompasses a wide variety of methods, each suited for different materials and applications. Understanding various welding techniques is crucial for professionals, hobbyists, and industries that depend on these methods to produce durable and high-quality products.
Among the most commonly used welding techniques are MIG (Metal Inert Gas) welding and stick welding, each with its unique set of advantages and purposes. MIG welding, known for its speed and versatility, employs a continuous wire feed and an inert shielding gas to protect the weld pool from contamination. On the other hand, stick welding, or arc welding, uses a coated electrode to create an arc that melts the filler material and the base metal simultaneously, making it an ideal method for outdoor applications and thicker materials.
When evaluating the strength of welds, it's essential to consider various aspects of Weld integrity factors, as they play a crucial role in the overall performance of the joint.
Welding techniques are not only pivotal in manufacturing but also in repair work; both MIG and stick welding have found their place in various industries such as automotive, construction, and shipbuilding. Professionals skilled in these techniques are highly sought after in the job market, as they contribute significantly to the quality and durability of welded structures. Evaluating the right technique depends on factors including material type, thickness, environmental conditions, and desired finish.
In the ongoing debate about welding techniques, it's essential to evaluate the strengths and weaknesses of each method to determine their suitability for various applications, especially when considering the welding joint comparison.
In addition to MIG and stick welding, other welding techniques like TIG (Tungsten Inert Gas) welding, flux-cored arc welding (FCAW), and laser welding are also important in modern applications. Each method has its specific characteristics, benefits, and drawbacks, making it essential for welders to choose the appropriate technique based on their project requirements. Recognizing the nuances between these welding techniques can significantly affect the outcomes of welding projects, making knowledge of each process invaluable for professionals and enthusiasts alike.
In the evolving world of welding technologies, advancements continue to emerge, leading to more efficient and effective welding procedures. Technologies such as robotic welding and automated systems are also being integrated into manufacturing practices, enhancing precision and productivity. As industries grow and needs change, continuous education and training in welding techniques remain a priority for those aiming to excel in the field.
Strength Comparison of MIG and Stick Welding
Understanding the strength of MIG welding involves evaluating its ability to produce strong, high-quality welds. MIG welding exhibits excellent penetration and consistent bead appearance, which contributes to its overall strength. The use of inert gas protects the weld pool from atmospheric contamination, reducing defects and enhancing the structural integrity of the welded joint.
Factors affecting MIG weld strength include the choice of filler material, gas flow levels, welding speed, and technique. Adjusting these parameters can improve the weld quality, allowing for a high strength-to-weight ratio in the finished product. Proper preparation, including surface cleaning and fit-up, also plays a significant role in ensuring a strong weld.
Comparatively, stick welding delivers robust welds, particularly in outdoor applications where wind or other environmental conditions can impede the shielding provided by gas in MIG welding. Stick welding's versatility also allows it to be effectively utilized on a variety of materials, including those that can be challenging to weld with MIG techniques. Ultimately, both welding methods have characteristics that can lead to strong welds, tailored to specific project requirements.
In the ongoing debate about welding techniques, understanding the unique properties and applications of each method can significantly impact the overall strength of your projects, especially when considering MIG vs. stick weld strength.
Applications of MIG Welding
Common uses of MIG welding in industries encompass automotive manufacturing, construction, and appliance production, where speed and versatility are vital. Its speed of operation allows for rapid production cycles, making MIG welding a preferred choice in high-volume environments. It is particularly effective for welding thin materials and providing a clean, professional finish.
Advantages of using MIG welding for thin materials include its ability to produce less heat distortion and a smoother finish, essential in applications where aesthetics and precision are critical. Additionally, MIG welding is highly adaptable to automation and mechanization, further enhancing its efficiency in industrial applications.
When to choose MIG welding over stick welding typically revolves around the need for speed, clean finishes, and the type of materials being welded. For projects that involve lighter gauge materials or require thin-section welds, MIG is often the ideal solution due to its ease of use and reduced cleanup requirements after welding.
Applications of Stick Welding
Durable applications for stick welding include heavy construction, shipbuilding, and pipeline laying, where strength and penetration are paramount. The ability to work in adverse conditions, such as high winds and open spaces, makes stick welding particularly advantageous for outdoor construction projects.
Best materials suited for stick welding include carbon steel, stainless steel, and some alloys, making it versatile for various industries. Since the flux from the electrode forms a protective layer over the weld pool, stick welding is not as affected by contaminants as other types, further broadening its applications.
Benefits of using stick welding in outdoor conditions stem from its portability and adaptability to environmental challenges. Stick welding does not require external shielding gas, thereby eliminating complications related to wind or weather, which can significantly affect MIG welding outcomes under similar conditions.
Welding Technique Differences
Comparing bead appearance in MIG vs. stick welding showcases fundamental differences in their finished products. MIG welding typically results in a more uniform and smooth bead with fewer visible imperfections, while stick welding may exhibit a broader and more textured bead due to the nature of the process.
The process of MIG welding is conducted by feeding a continuous solid wire electrode through the welding gun while simultaneously supplying an inert shielding gas. As the wire melts upon contact with the workpiece, a weld pool forms, creating a joint as the filler material solidifies. This continuous feed allows for rapid welding, making it efficient in various applications.
The process of stick welding is characterized by the creation of an electric arc between a coated electrode and the metal being welded. The heat from the arc melts both the filler rod and the base material, forming a molten pool. As the weld cools, the coating on the electrode burns away, providing shielding to protect the weld from contaminants, unlike the inert gas utilized in MIG welding.
Welding Safety Practices
Safety measures for MIG welding are crucial due to the presence of high heat and shielding gases. Proper ventilation, using a filtration system, and ensuring the workspace is free from flammable materials help mitigate risks. Additionally, maintaining equipment regularly ensures safety and functionality during operations.
Safety considerations for stick welding involve wearing protective gear to shield against UV radiation and flying sparks. Proper grounding of equipment prevents electrical hazards, while awareness of surroundings can prevent accidents during the welding process.
Protective gear for both MIG and stick welding includes helmets with appropriate lens darkness, gloves, flame-resistant clothing, and proper footwear. These ensure the operator remains safe from burns, electrical shocks, and other hazards associated with welding activities.
Cost Analysis of Welding Methods
Cost comparison of MIG vs. stick welding reveals different economic implications for each technique. Generally, MIG welding equipment tends to have a higher initial investment compared to stick welding setups due to additional components, such as gas regulators and wire feeders. However, the speed and efficiency of MIG can lead to lower operational costs in high-production environments.
Long-term expenses associated with MIG welding include costs related to gas supplies, wire feed, and maintenance of more complex machinery. Understanding these ongoing costs is essential for businesses that rely on these methods for production and fabrication.
Initial investment considerations for stick welding are relatively lower, making it an attractive option for small businesses or hobbyists. Its simplicity and portability contribute to minimal setup costs, while its ability to perform well outdoors can reduce additional expenses when working in challenging environments.
Learning Curve for MIG and Stick Welding
Time required to learn MIG welding is often shorter compared to stick welding due to its user-friendly setup and less complex techniques. Most beginners can become proficient with MIG in a few hours of practice, making it an appealing option for those new to welding.
Time required to master stick welding varies, as it often requires more skill and experience to produce high-quality welds consistently due to the manipulation of rods and controlling arc length. Mastery may take weeks to months of dedicated practice, particularly for intricate applications.
Resources for training in both welding methods include vocational schools, online courses, and hands-on workshops offered by community colleges and technical institutes. Practical experience paired with theoretical knowledge helps aspiring welders gain the confidence and skills necessary to excel in their chosen techniques.