Explore Common Arc Welding Techniques and Their Applications
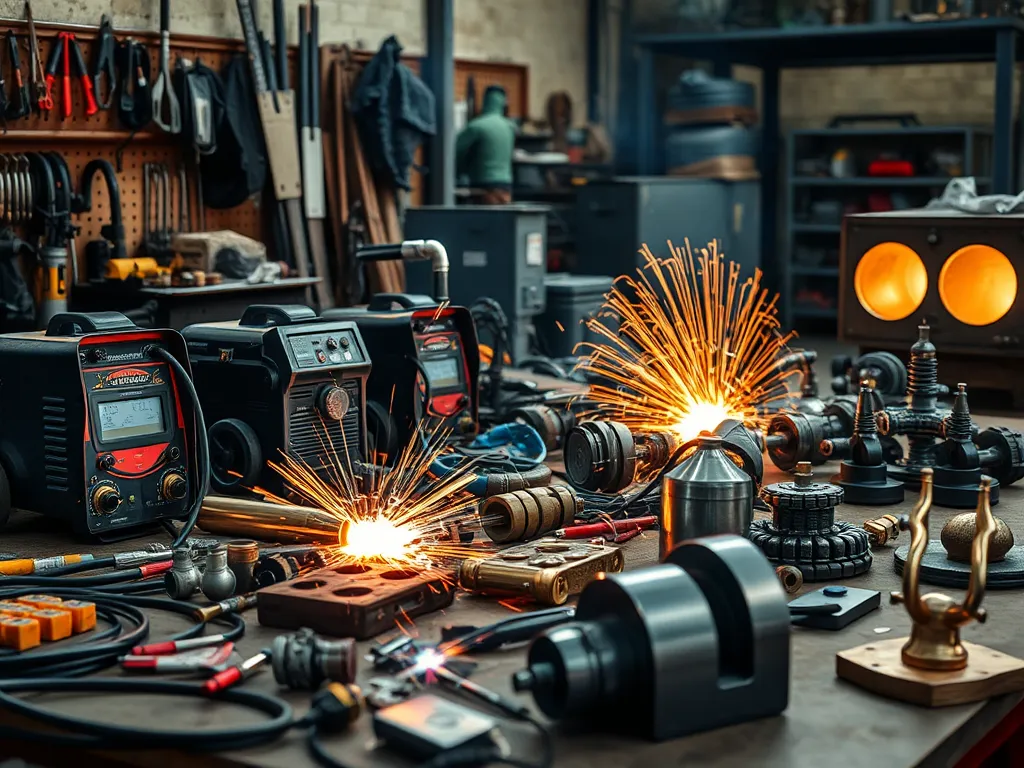
Common Arc Welding Techniques and Their Applications
Arc welding has transformed the landscape of manufacturing and construction, providing a reliable way to fuse metal pieces together. Common Arc Welding Techniques and Their Applications are vital in various industries, enabling the creation of strong joints for structural components, pipelines, and many other metal assemblies. Understanding these techniques can help businesses choose the right method for their specific needs and projects.
In high-precision applications, TIG welding stands out for its ability to produce clean and aesthetically pleasing welds.
In essence, arc welding utilizes an electric arc to generate heat that melts the base materials and forms a welded joint. Different techniques have emerged, each with unique processes and applications that make them suitable for various scenarios. This article will delve into the most popular arc welding methods, their processes, materials best suited for each technique, and common applications in industries ranging from construction to manufacturing.
The primary techniques of arc welding include Shielded Metal Arc Welding (SMAW), Gas Metal Arc Welding (GMAW), Gas Tungsten Arc Welding (GTAW), Flux-Cored Arc Welding (FCAW), and Submerged Arc Welding (SAW). Each method varies in terms of equipment required, the skill level needed, and types of materials that can be welded. In an industry where efficiency and strength are paramount, understanding these differences is crucial for making informed decisions.
Utilizing submerged arc welding can significantly boost productivity and quality in large-scale industrial projects.
Moreover, the advancements in arc welding technologies and equipment have led to improved quality and efficiency in welding processes. Automation in welding has also paved the way for precise and repeatable welds, which are crucial for critical applications such as aerospace, automotive, and energy. As industries grow and evolve, the role of arc welding techniques continues to expand, making them essential knowledge for engineers and industry professionals.
In summary, the Common Arc Welding Techniques and Their Applications play a pivotal role in manufacturing and construction. By exploring different techniques, their benefits, and applications, businesses can enhance their production capabilities and ensure the quality and reliability of their welded products.
Shielded Metal Arc Welding (SMAW)
Shielded Metal Arc Welding (SMAW), also known as stick welding, is one of the oldest and most common methods of arc welding. In SMAW, an electric arc forms between a coated electrode and the base metal, creating the heat necessary to melt both the electrode and the base material, forming a molten weld pool. The coating on the electrode serves to shield the weld area from contaminants in the air which can affect weld quality.
SMAW is versatile and can be used with various materials, including carbon steel, stainless steel, cast iron, and certain non-ferrous alloys. It is most effective on materials of medium thickness and can be used in various positions, making it ideal for fieldwork and construction sites where accessibility might be limited.
Common applications of SMAW in industries include pipeline construction, shipbuilding, and the fabrication of heavy equipment. It is preferred in maintenance and repair tasks due to its portability and the simplicity of the equipment involved.
For strong and durable metal joints, professionals often choose stick welding due to its versatility and efficiency.
Gas Metal Arc Welding (GMAW)
Gas Metal Arc Welding (GMAW), often referred to as MIG (Metal Inert Gas) welding, utilizes a continuous solid wire electrode fed through a welding gun. During the welding process, a shielding gas (typically argon or a mixture of gases) is simultaneously released to protect the molten weld pool from atmospheric contamination. This process allows for high deposition rates and smooth welds.
The benefits of using GMAW include faster welding speeds, reduced overall labor costs, and a clean, low-spatter finish. It is also relatively easier to learn than other arc welding methods, making it suitable for both beginners and experienced welders alike.
GMAW is commonly utilized in the automotive industry, light fabrication, and any applications requiring high-speed welding of lighter materials such as aluminum and thin steel sections. Its ability to automate the welding process makes it a favorite for both assembly line production and custom projects.
Gas Tungsten Arc Welding (GTAW)
Gas Tungsten Arc Welding (GTAW), known as TIG (Tungsten Inert Gas) welding, is characterized by the use of a non-consumable tungsten electrode to produce the weld. The welder must manually feed a filler rod into the weld pool, and an inert gas, often argon, protects the weld from contamination. GTAW is often used when high precision and aesthetic quality are required.
The advantages of GTAW include exceptional control over the welding arc and heat, making it ideal for thin materials and intricate welds. It produces high-quality welds free of spatter, which can be essential in applications where appearance matters.
Industries where GTAW is most applicable include aerospace, automotive, and high-purity applications such as food processing and pharmaceutical equipment. Its versatility and precision make it essential for manufacturing components that meet strict quality standards.
Flux-Cored Arc Welding (FCAW)
Flux-Cored Arc Welding (FCAW) is similar to GMAW but uses a tubular wire filled with flux instead of a solid wire. This flux generates a shielding gas when exposed to heat, providing protection to the weld from contamination. FCAW can be used with or without an external shielding gas, offering flexibility depending on the application.
Key advantages of FCAW include high deposition rates and the ability to produce welds in windy conditions without the need for additional shielding gas. It allows for deeper penetration and is particularly effective on dirty or rusty materials, providing a strong bond even in less-than-ideal conditions.
Common uses of FCAW are found in construction and repair applications, especially in heavy equipment repair, shipbuilding, and structural welding. Its effectiveness on thicker materials makes it a preferred choice for projects requiring strong, enduring welds.
Submerged Arc Welding (SAW)
Submerged Arc Welding (SAW) is an automatic or semi-automatic welding process where an arc forms between a continuously-fed electrode and the workpiece, while the molten weld pool is submerged under a layer of granular flux. This flux not only shields the weld area but also stabilizes the arc and helps to clean the base metal.
The benefits of using SAW for thick materials are profound; it produces deep penetration welds, allowing for effective bonding in just a single pass, and creates welds with minimal spatter, reducing the need for post-weld cleanup. It is also well-suited for high-production work, leading to faster throughput times.
Specific applications of SAW are often found in heavy industries such as shipbuilding, oil and gas pipeline construction, and the manufacturing of large structural components. Its efficiency and effectiveness make it a top choice for projects requiring high-volume production and supreme strength in welds.