Maximizing Construction Efficiency for Welding Projects
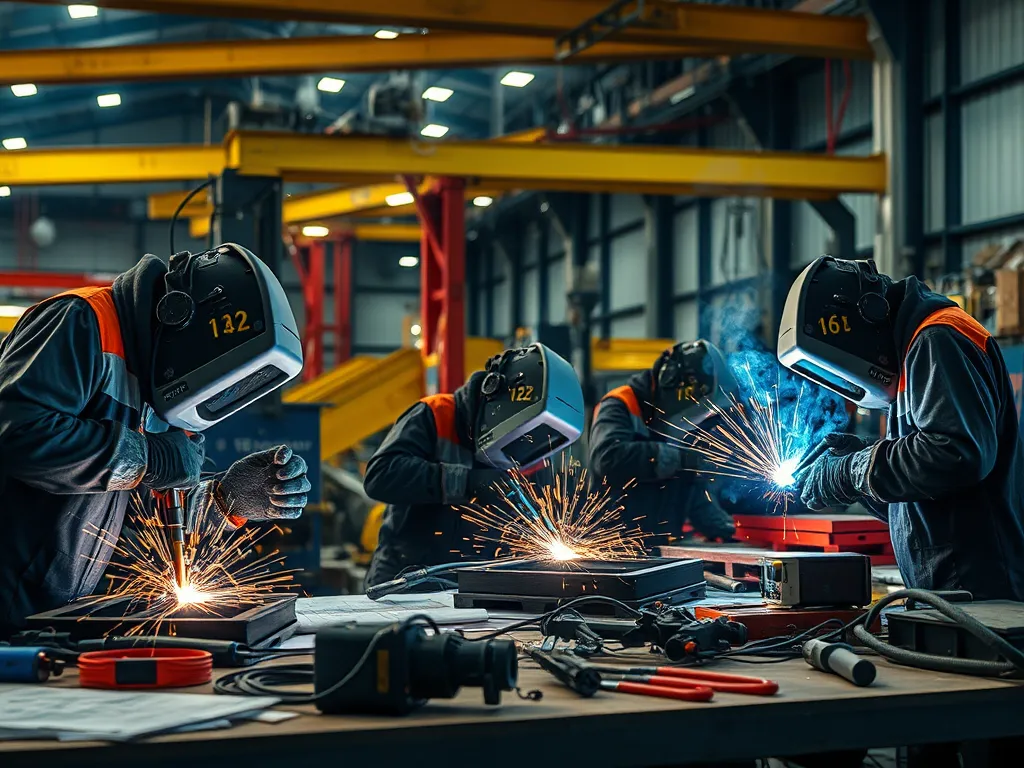
Enhancing Construction Efficiency for Welding Operations
Construction efficiency for welding is an essential aspect that impacts overall project timelines, costs, and the quality of the final product. With advancements in technology and methodologies, achieving high levels of construction efficiency for welding tasks is more attainable than ever. By optimizing processes, embracing innovation, and ensuring quality control, construction managers can significantly improve welding efficiency, reduce rework, and enhance safety on job sites.
Our experts deliver On-location welding solutions tailored to meet your specific project requirements.
One of the crucial factors contributing to construction efficiency for welding is the integration of modern technologies. Automated welding processes, such as robotic welding, have revolutionized how welding is approached in construction projects. Automation reduces the time needed for welding tasks while maintaining high-quality standards, leading to considerable time and cost savings. This shift towards automation allows skilled labor to focus on more complex tasks, thereby improving overall efficiency.
For any emergency, our team offers 24/7 welding assistance ensuring your operations never halt.
Additionally, employing welding robots elevates construction efficiency for welding by ensuring precision and repeatability in welds. These robots can perform multiple tasks with consistent quality, thus reducing the incidence of defects. Furthermore, they can work longer hours without fatigue, leading to quicker project completion. Their integration into construction workflows allows teams to optimize their labor force and allocate human resources more effectively.
To enhance construction efficiency for welding, it is essential to adopt advanced welding methodologies. Techniques such as laser welding, TIG (Tungsten Inert Gas) welding, and MIG (Metal Inert Gas) welding are giving way to innovative practices that ensure strong, clean welds in less time. These methodologies are particularly useful in construction environments where speed and quality are paramount. By implementing these techniques, construction teams can significantly expedite the welding phase of projects, enhancing overall efficiency.
Lastly, effective scheduling practices are instrumental in promoting construction efficiency for welding. By organizing welding tasks within the broader construction timeline and coordinating them with other activities, project managers can minimize downtime and optimize resource allocation. Establishing a clear and efficient schedule enables teams to respond to challenges proactively, ensuring that welding processes integrate smoothly into the overall construction workflow.
Techniques to Improve Welding Efficiency
Automated welding processes have become a game-changer in improving welding efficiency. By employing sophisticated machinery that executes welding tasks with precision and speed, companies can reduce labor costs and increase throughput. Automation allows for consistent results, which are crucial for maintaining weld quality and meeting project deadlines.
Employing welding robots has proven to be a pivotal factor in enhancing construction efficiency for welding. These machines handle repetitive tasks with high accuracy and can operate in challenging environments where manual welding might be impractical. The use of robots reduces the risk associated with human error and enhances productivity, allowing for quicker project completions without compromising on quality.
Advanced welding methodologies are constantly evolving, enabling construction projects to achieve greater efficiency. Techniques such as friction stir welding and plasma arc welding introduce innovative approaches to joining materials. These modern methodologies allow for stronger and more reliable welds, ultimately reducing the need for rework and inspection, thus streamlining the entire construction process.
Experience quick and efficient Rapid response repairs for all your equipment needs.
Effective scheduling practices are crucial for managing welding tasks within broader construction timelines. By properly aligning welding operations with other site activities, project managers can ensure resources are used efficiently and that welding teams are working at optimal times, thereby decreasing waiting periods and enhancing productivity.
Quality Control in Welding
Monitoring weld quality standards is a vital part of ensuring construction efficiency for welding. Establishing strict guidelines for weld quality helps in detecting issues early in the process, reducing the likelihood of defects that can lead to costly rework. Consistent quality monitoring ensures that all welds meet predetermined standards and helps maintain overall project integrity.
Defect detection methods play a critical role in quality control for welding. Techniques such as ultrasonic testing, radiographic inspection, and visual examination are essential for identifying flaws in welds before they escalate into more significant problems. Early defect detection helps ensure that construction efficiency is not impacted by the need for extensive repairs down the line.
Training for weld inspectors is paramount in maintaining high-quality standards. Well-trained inspectors can effectively identify issues and enforce quality control measures. Investing in training ensures that inspectors are familiar with the latest welding technologies and methodologies, further supporting construction efficiency by upholding rigorous quality standards.
Implementing quality assurance processes is essential in welding operations. A robust quality assurance framework involves regular checks and audits of welding practices, ensuring compliance with industry standards. This systematic approach to quality guarantees that construction efficiency is upheld through consistent, high-quality outputs.
Welding Materials and Their Impact
Selecting the right welding materials is foundational to construction efficiency for welding. The choice of alloys and filler materials can significantly influence the weld's strength, durability, and resistance to environmental factors. Careful material selection aligned with project requirements leads to fewer failures and enhanced operational efficiency.
The effects of material preparation before welding cannot be overstated. Properly preparing the materials, including cleaning, fitting, and preheating if necessary, plays a significant role in achieving strong welds. Well-prepared materials minimize issues related to contamination and misalignment, thereby promoting better overall efficiency in welding processes.
Compatibility of materials in welding is critical. Ensuring that the chosen materials can be effectively joined through welding processes is vital for structural integrity. A mismatch in material properties can lead to weld failures, which not only affects project timelines but can also lead to increased costs due to rework and repairs.
The impact of material quality on efficiency is profound. High-quality materials translate to higher-quality welds and, consequently, more efficient construction processes. Investing in superior materials minimizes the risk of defects and helps streamline construction workflows, ultimately leading to increased productivity and cost-effectiveness.
Project Management in Welding Construction
Planning and resource allocation is key to enhancing construction efficiency for welding. Proper planning allows project managers to anticipate challenges and allocate resources effectively, ensuring that welding operations are executed smoothly and without unnecessary delays. This proactive approach leads to better utilization of time and labor resources.
Scheduling for welding tasks requires careful coordination with other construction activities. Effective scheduling allows welding teams to work efficiently without interruptions, and ensures that waiting periods are minimized. By synchronizing welding operations with the overall construction schedule, project managers can optimize workflow and enhance productivity.
Risk management in welding projects is crucial for maintaining construction efficiency. Identifying potential risks early and implementing mitigation strategies helps prevent delays and ensures that the welding process runs smoothly. Effective risk management is essential for sustaining efficiency and meeting project deadlines.
Communication strategies among teams play a significant role in construction efficiency for welding. Clear communication ensures that all team members are aligned on goals and responsibilities, reducing the likelihood of misunderstandings and errors. Establishing effective communication channels fosters collaboration and ensures a streamlined workflow on construction sites.
Safety Practices in Welding Operations
Implementing safety protocols is paramount in welding operations to protect workers and enhance construction efficiency. Establishing clear safety guidelines helps reduce the risk of accidents and ensures that all team members are aware of best practices, which promotes a safe and efficient work environment.
Training for safe welding practices is essential for maintaining a culture of safety on construction sites. Well-trained welders are more likely to adhere to safety protocols, reducing the risk of injuries and enhancing overall project efficiency. Regular training sessions help reinforce the importance of safety in welding operations.
The use of protective equipment is critical in safeguarding welders against potential hazards. Ensuring that all personnel have access to proper protective gear, such as helmets, gloves, and aprons, mitigates risks and fosters a safe working environment. This focus on safety enhances efficiency by minimizing downtime related to accidents or injuries.
Emergency response planning for construction sites is a crucial component of safety practices. Preparing for potential accidents and having a well-defined emergency plan facilitates a quick response in case of incidents. This preparedness not only protects workers but also minimizes disruptions in workflow, thereby supporting construction efficiency.