Understanding Arc Welding: A Comprehensive Guide
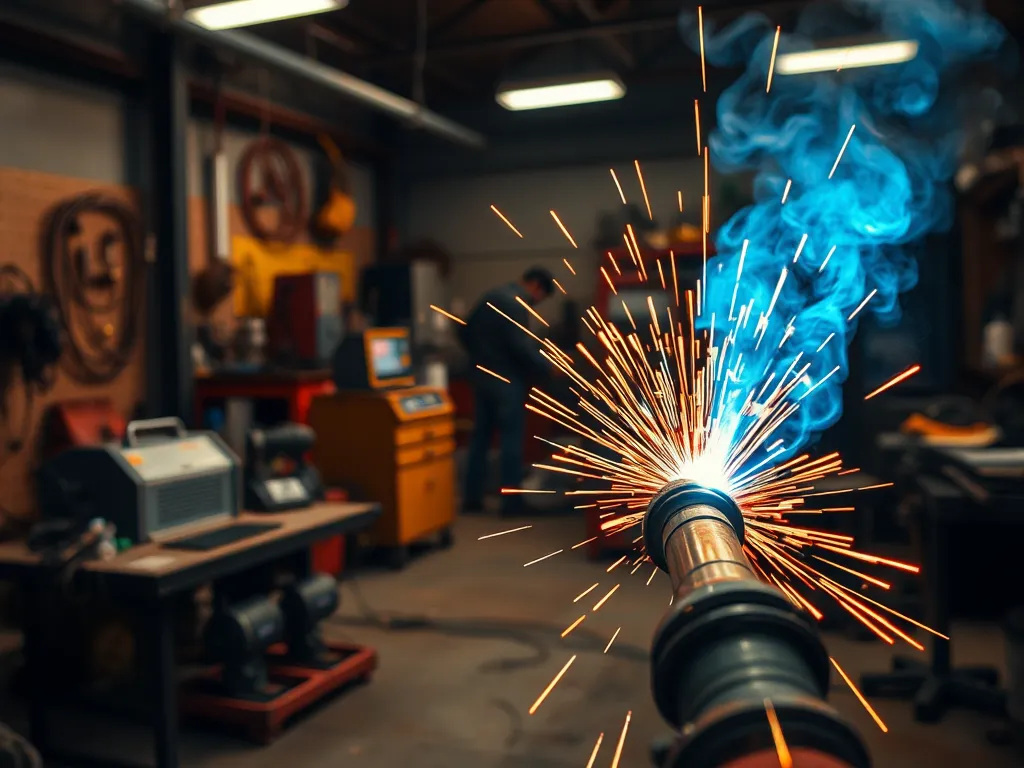
A Comprehensive Guide to Arc Welding
Arc Welding is a pivotal process in the field of metal joining that utilizes an electric arc to melt and fuse metals together. This method has become essential across various industries due to its efficiency and versatility. The arc creates a high-temperature environment, allowing for the welding of metals ranging from thin sheets to heavy structural components.
The process of Arc Welding involves generating an electric arc between an electrode and the workpiece, producing sufficient heat to melt the metal. The molten metal then cools and solidifies, forming a strong bond between the parts. Different forms of Arc Welding have been developed, each suited to particular applications and materials, enhancing the overall quality and strength of the weld.
This guide on how to arc weld offers practical tips for beginners.
Safety is a paramount concern in Arc Welding, with operators required to wear protective gear to shield against harmful rays, metal splatters, and exposure to intense heat. Understanding arc welding techniques and equipment is essential for ensuring effective and safe welding practices. With the right knowledge, technicians can minimize risks while achieving high-quality welds.
For those wondering what is arc welding, this resource explains the basics.
In the following sections, we will delve deeper into the basics, types, characteristics, applications, advantages, and limitations of Arc Welding to provide a comprehensive understanding of this essential welding method.
Whether for industrial manufacturing or artistic metalwork, Arc Welding remains a critical skill that combines science with creativity, making it one of the most valuable techniques in modern metal fabrication.
If you're interested in arc welding, you'll find top-notch services here.
The Basics of Arc Welding
Arc Welding can be defined as a process that uses an electric arc to generate heat for melting two metals together. The basic principle is to create an electric arc between an electrode and the workpiece, which produces sufficient heat to melt the metal at the joint. This method is commonly used for both ferrous and non-ferrous materials and is recognized for its ability to produce strong welds.
The history of Arc Welding dates back to the late 19th century, when it was first developed as a method to join metals using the heat of an electric arc. In 1881, electric welding was demonstrated in Russia, and by the early 1900s, the process had evolved significantly. The introduction of various electrodes and shielding techniques throughout the 20th century led to advancements that made Arc Welding safer and more efficient, ultimately leading to its widespread adoption in manufacturing.
Arc welding equipment consists of several components, including a welding machine, electrodes, and a workpiece. The welding machine generates the electrical current required to create an arc, while the electrodes provide the filler material needed for the weld. Additionally, shielding gas may be used in specific processes to protect the molten metal from contamination, ensuring the integrity and quality of the weld.
Types of Arc Welding Processes
One of the most common types of Arc Welding is Shielded Metal Arc Welding (SMAW), often referred to as stick welding. This process involves a consumable electrode that is coated with flux to protect the weld from contaminants. SMAW is highly versatile and suitable for a wide range of materials and thicknesses, making it a preferred method in construction and repair work.
Another prominent type is Gas Tungsten Arc Welding (GTAW), also known as TIG welding. Using a non-consumable tungsten electrode, this process allows for precise control over the welding arc. GTAW is ideal for thin materials and offers excellent quality welds, commonly used in industries such as aerospace and automotive manufacturing.
Gas Metal Arc Welding (GMAW), or MIG welding, employs a continuous wire feed as an electrode and shielding gas to protect the weld area. This process is known for its speed and ease of use, making it popular for high-volume production and fabrication applications. GMAW is effective for welding various metals, including aluminum and stainless steel.
Arc Characteristics and Their Importance
Understanding electrical arcs is crucial for effective welding. The arc temperature can exceed 6,500 degrees Fahrenheit, which allows for the melting of metals at the joint. Various factors, such as the type of electrode, voltage, and current settings, influence the stability and characteristics of the arc, significantly affecting the quality of the weld.
Several factors affect arc stability, including electrode angle, distance from the workpiece, and the type of materials being welded. Maintaining a stable arc is essential for achieving uniform penetration and minimizing defects in the weld. Proper training and experience help welders adjust these parameters effectively, ensuring optimal results.
Safety measures are fundamental during arc welding. Welders must wear protective gear, such as helmets, gloves, and protective clothing, to shield against harmful UV radiation, heat, and sparks. Adequate ventilation is also necessary to minimize exposure to hazardous fumes generated during the welding process, ensuring a safe working environment.
Applications of Arc Welding
Arc Welding finds extensive application in various industries, particularly in manufacturing and construction. It is used to fabricate and repair machinery, bridges, ships, and pipelines. The ability to weld thick sections of metal quickly makes it ideal for heavy-duty structural applications.
In construction and fabrication, Arc Welding is essential for building frameworks, structural components, and even decorative elements. The process facilitates the joining of steel beams, rebar, and metal decking, contributing significantly to the structural integrity of buildings and infrastructure.
The automotive industry heavily relies on Arc Welding for manufacturing vehicles. With the ability to produce strong, durable welds, it is used in assembling car frames and body panels. Advanced welding techniques, such as robotic MIG welding, enable efficient production lines, ensuring high-quality and consistent results.
Advantages and Disadvantages of Arc Welding
The benefits of using Arc Welding include versatility, efficiency, and the ability to weld a wide range of materials. It is a widely accessible welding method, often requiring less costly equipment compared to other welding processes. Additionally, the process can be performed in various environments, making it ideal for repair work and field applications.
However, Arc Welding does have limitations compared to other welding methods. It can be more challenging to master, requiring skilled operators to manage the arc effectively. Additionally, some processes may produce a significant amount of heat, which can lead to warping or distortion of thin materials if not managed properly.
Cost efficiency is another factor to consider with Arc Welding. While initial equipment costs may be lower, the operational costs can increase due to the need for skilled labor and potential material waste. Careful planning and training are essential to optimizing efficiency and minimizing costs in Arc Welding operations.